
Non Destructive Testing (NDT) is a descriptive term used for the examination of materials and components in such a way that allows materials to be examined without changing or destroying their usefulness. NDT can be used to locate and size surface and subsurface flaws and defects. NDT plays a crucial role in everyday life and is necessary to assure safety and reliability. Typical examples are found in aircraft, ships, motor vehicles, pipelines, bridges, trains, power stations, refineries, buildings and oil platforms which are all inspected using NDT methods. NDT is a Quality Assurance management tool which can give impressive results when used correctly. It requires an understanding of the various methods available, their capabilities and limitations, knowledge of the relevant standards and specifications for performing the tests. Materials, products and equipment which fail to achieve their design requirements or projected life due to undetected defects may require expensive repair or early replacement. Such defects may also be the cause of unsafe conditions or catastrophic failure, as well as loss of revenue due to unplanned plant shutdown. Non Destructive Testing can be applied to each stage of an item's construction. The materials and welds can be examined using NDT and either accepted, rejected or repaired. NDT techniques can then be used to monitor the integrity of the item or structure throughout it's design life.
NDT is typically used for the following reasons
- To determine acceptance to a required Standard (e.g. Welded Structures)
- To improve product reliability (e.g. Castings & Forgings)
- Component failure prevention as a part of Condition Monitoring (e.g. Mandatory inspection of cranes & Platforms)
- To provide condition assessment for development of repair criteria (e.g. Mid-Life refurbishment of installed machinery)

In accordance with AS1171 inspections can be performed on all magnetic metals for surface breaking and near surface discontinuities, these can be in the form of weld defects in fabrications, production faults in castings and forgings or in-service fatigue cracks in all three. For inspection, components must be in bare metal condition and cleaned of heavy surface corrosion, dirt and other contaminants. Inspections can be performed under daylight conditions (black on white contrast) or for greater sensitivity, using fluorescent particles, in low light conditions under high intensity Ultra Violet lighting.
Common items requiring Magnetic Particle Testing (MT) include:
- Welded fabrication requiring compliance to AS1554, AS4307, AS1210 etc.
- New casting and forgings
- Cranes, Scissor and Boom Lifts during Ten Yearly inspection and re-certification as per AS2550
- In service inspections of critical infrastructure subject to dynamic loads and stresses including Power Generation, Water Supply and Transport infrastructure
- Motor vehicle components during overhaul, rebuild or restoration, including engine blocks, heads, crankshafts and suspension components
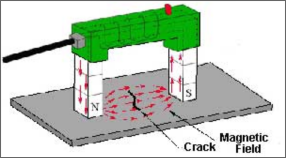

In accordance with AS2062 inspections can be performed on all non-porous materials for surface breaking flaws, these can be in the form of weld defects in fabrications, production faults in castings and forgings or in-service fatigue cracks in all three. PT inspection is primarily used on non-magnetic steels (300 series Stainless steels, Aluminium, Bronze, etc.) and non-metals. For inspections, components must be in bare metal condition and cleaned of heavy surface corrosion, dirt and other contaminants. Inspections can be performed under daylight conditions (red on white contrast) or for greater sensitivity, using fluorescent particles, in low light conditions under high intensity Ultra Violet lighting.
Common items requiring Dye Penetrant Testing (PT) include:
- Welded fabrications requiring compliance to AS1554, AS4307, AS1210 etc.
- New Non-Ferrous castings and forgings
- In service inspections of non-magnetic critical infrastructure subject to dynamic loads and stresses including Power Generation, Water Supply and Transport Infrastructure
- Motor vehicle components during overhaul, rebuild or restoration, including aluminium engine blocks, heads and alloy wheels
- Leak testing on welded vessels and fluid tight castings
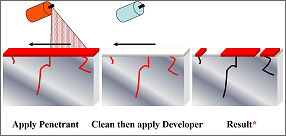
C & M Blake Engineering Services
NON DESTRUCTIVE TESTING
MECHANICAL DRAFTING
Blake Holdings Pty Ltd
ABN: 81 603 672 000
26A Sunways Avenue
Seven Mile Beach
Hobart, Tasmania 7170
Call Chris for information
Tel: 0477 862 009
:
Christopher Blake, owner of
C & M Blake Engineering Services has been a part of the
Tasmanian engineering community for over thirty years, as a fitter and turner he has worked for
- Hydro Tas - manufacturing power generation components
- APCO Engineering - Specialist Marine Products manufactureer
- ACME Engineering - Precision machining, Design & Heat Treatment
During this time he has gained skills in all aspects of the trade, working with conventional machine tools of all sizes, programming and operating Computer Numerical Controlled machines, Electro-Discharge Machines and precision gear and spline manufacturing.
In addition to traditional Fitting and Machining, Christopher has also had extensive experience in the Heat Treatment of steels, assembly and testing of large Hydro Turbine components and using Computer Aided Drafting for design and production of component drawings for manufacture.
Since 2008 Christopher has moved away from the workshop and has been Planning and Co-ordinating manufacture and refurbishment projects for Alstom Power Services. A further stage in this engineering career has been to undergo training in the field of Non-Destructive Testing, being qualified in both Magnetic Particle and Dye Penetrant methods and gaining Level 2 Certification to practice with the Australian Institute of Non Destructive Testing (AINDT)
Current Licences and Permits
- L2 MT & PT (AS3998/ISO9712)
- AINDT - CB# 4679
- Construction Industry White Card
- Hydro Tas Level 2 Instructed Person
- First Aid & CPR
- Confined Space Entry
- Yellow Card EWP - boom lift & scissor lift <11 metres
- High Risk Licence - Fork Lift
- Tasmanian Driver's Licence